Future Food Tech
Future-proofing cultivated seafood: Addressing supply chain hurdles for the next decade
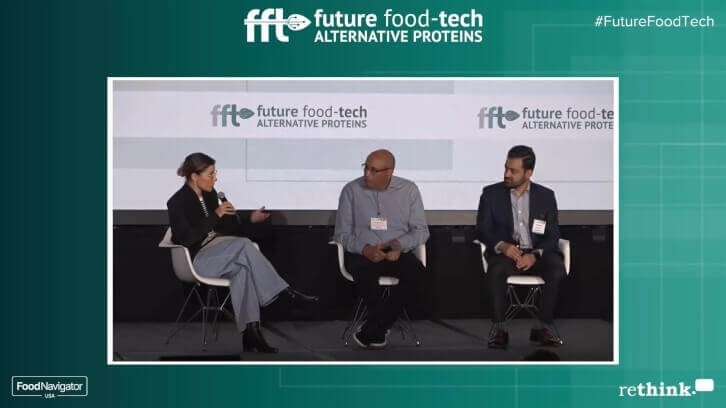
As the global seafood industry faces significant challenges due to overfishing, pollutants, climate change and food safety regulations, cultivated seafood promises a consistent and sustainable source of protein, help to restore oceans and reduced contamination risks in the food supply. However, several hurdles exist throughout the cultivated seafood supply chain:
- Infrastructure limitations: Large-scale facilities to produce cultivated seafood are scarce.
- Fragile raw material supply: Growth media, essential for cultivating seafood, is both expensive and difficult to produce in sufficient quantities.
- Distribution challenges: Existing distribution networks may not be optimized for the specific needs of cultivated seafood.
- Scalability limitations: Current technology cannot produce cultivated seafood at commercially viable volumes.
Blue Nalu and Umami Bioworks are addressing these supply chain challenges, demonstrating the potential of their cultivated seafood products in foodservice and indicating how this innovation can be adopted mainstream.
Identifying seafood’s unique challenges
Based in San Diego, Calif., Blue Nalu is preparing to cultivate bluefin tuna toro in a 140,000 square-foot facility, designed to produce up to six million pounds of premium seafood annually using eight 100,000-liter terminal bioreactors. Bluefin toro is considered a highly prized species with a premium price across global markets.
"Seafood has unique challenges," said Lou Cooperhouse, founder, president and CEO, Blue Nalu.
"It is imported into the United States at up to 85%, and wild catch fisheries have been flat for about four decades. Aquaculture has limitations as only certain species can be grown that way, and growing seafood in close proximity poses challenges. Moreover, warming oceans, acidification and climate change disrupt our supply chain, making quality inconsistent. Pregnant women and young children must limit seafood intake due to high mercury levels. Cultivated seafood offers a solution with food security, consistency, accessibilityand health benefits."
Headquartered in Singapore, Umami Bioworks focuses on the global seafood supply chain, especially in Southeast Asia, where 70% of the supply chain is located and three billion people rely on fish as their primary protein source, Mihir Pershad, the company’s CEO explained.
"It's a global problem affecting nearly half the population," he said. "We need reliable seafood supply because many people rely on it as a crucial food source. Hundreds of species are endangered or protected yet still illegally caught in significant volumes. Consumers are willing to pay high prices for rare species like snapper, tuna, or eel, unlike beef, pork, or chicken."
Despite the hurdles, the cultivated seafood sector has grown significantly over the last six years.
Cooperhouse noted that while the biology, scalability, regulatory environment, supply chain and profitability were unknown six years ago, there have been substantial advancements.
"We now have regulatory approval in three nations, established food-grade supply chains, animal component-free media and scalable cell lines. We are a few years away from seeing cultivated seafood in the market at a reasonable volume, likely by 2030,” he said.
‘It is impossible for startups to achieve this alone’
Umami Bioworks' patented modular, standardized and automated production platform, CultivateOS, ensures scalability, transparency, and cost-effectiveness for traditional seafood companies. The platform packages and delivers the value chain of “cell line, media and process IP for manufacturers,” Pershad said.
He noted that the “plug and play” bioprocessing method may be more viable to work with as it allows for ingredient suppliers to “select and formulate the right combination of media grades.”
He continued, "It’s impossible for startups to achieve this alone. Our B2B approach involves strategic traditional incumbents from the seafood industry in our commercialization path, so we are not building our first factory alone.”
Localizing production models – a pathway to global commercialization?
Does the path to a global supply chain start with local efforts? Cooperhouse referred to vertical farming as an example of an industry built close to population centers, producing a 100% local yield.
"It all begins with market opportunity," he said. "This is difficult and challenging. Both of our companies are working with high-value products that have a strong presence in Asia. Yes, we may build our first factory in the US, but we might also build in Asia or the Middle East. It depends on where market demand is greatest and where addressing food security is most crucial."
Singapore demonstrates a localized production and distribution model with cultivated meat available in grocery stores.
Pershad added that as a smaller country, Singapore excels in "leaning into the sandbox approach of figuring out how to do something interim, recognizing and publicizing that it is a first of its kind, and learning along the way. Larger governments are typically adverse to publicly admitting they made a mistake."
He highlighted that food safety laws in Singapore are being "rewritten to accommodate new innovations," though it remains a multi-year effort. In contrast, the US is "pretty food secure at a national level," often seen in the overproduction of food, while Singapore faces geographical limitations, like limited arable land, that make food security a national security issue, thus receiving significant government attention.
"There are different approaches depending on the urgency of the problem for each country," he said.